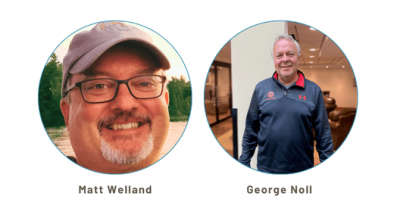
Written by Matt Welland – “Key Account Manager”
& George Noll -“Technical Sales Representative – Retired“
Aug. 14, 2024
Cooling water is essential in numerous industrial applications, providing a vital service in maintaining optimal operating temperatures for process fluids or steam. The efficiency and reliability of cooling systems are paramount, whether through once-through cooling, cooling towers, or open recirculating systems. Each method presents unique challenges and requires meticulous management to ensure system integrity and performance.
What you’ll learn:
Potential for Leaks in Once-Through Cooling Water Heat Exchangers.
Corrosion and Scaling of Cooling Water System Components.
Biological Contamination in Cooling Tower Water.
Release of Hydrocarbon Vapors in Cooling Tower Water.
Controlling Cooling Tower Water Chemistry
Potential for Leaks in Once-Through Cooling Water Heat Exchangers.
Once-through cooling systems utilize large volumes of water, often sourced from rivers, lakes, or wells, to absorb heat from industrial processes. These systems are efficient but present a significant risk of leaks. Heat exchangers in once-through systems can develop leaks, leading to water loss and potentially contaminating the process fluids. Identifying and addressing leaks promptly is crucial to prevent operational disruptions and environmental impact.
Secure your cooling systems with Novatech’s proprietary Hydrocarbon Sparger Technology. Engineered for rapid and accurate hydrocarbon detection, this system is adaptable with various gas detectors and analyzers.
Corrosion and Scaling of Cooling Water System Components.
Corrosion and scaling are persistent issues in cooling water systems. Corrosion can weaken system components, leading to failures and costly repairs. Scaling, caused by the precipitation of dissolved minerals, can reduce heat transfer efficiency and block water flow. Effective water treatment strategies, including the use of corrosion inhibitors and scale preventatives, are essential to maintaining system performance and longevity.
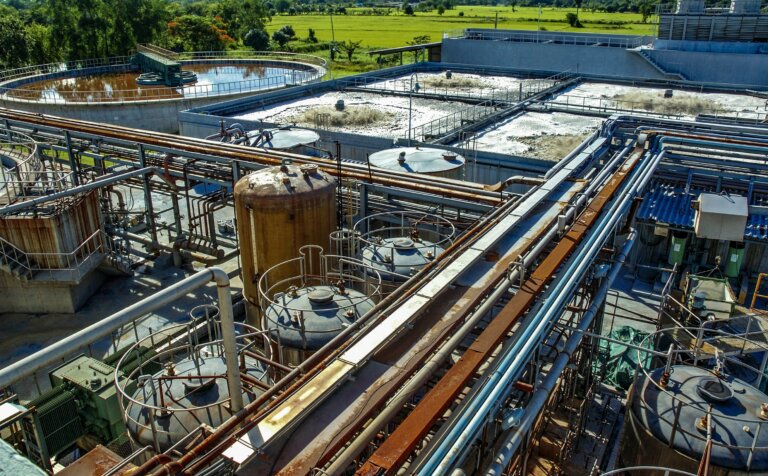
Biological Contamination in Cooling Tower Water.
Cooling towers that dissipate heat through evaporation are prone to biological contamination. Warm, moist environments are ideal for microbial growth, leading to biofilm formation and potential health risks. Regular monitoring and treatment of cooling tower water are necessary to control biological contamination. Biocides and other water treatment chemicals help maintain a clean system and ensure safe operation.
Optimize your cooling system with INOV8‘s GPP Controller. This advanced analyzer detects oil leaks and monitors environmental parameters with precision, using RapidWave Ultrasonic Cleaning and Laser-Induced Fluorescence.
Release of Hydrocarbon Vapors in Cooling Tower Water.
In chemical and hydrocarbon processing industries, cooling tower water can become contaminated with hydrocarbon vapours. These contaminants can pose safety hazards and environmental risks if released into the atmosphere. Monitoring and controlling hydrocarbon levels in cooling tower water are critical to prevent vapour release and ensure compliance with environmental regulations.
Controlling Cooling Tower Water Chemistry.
Maintaining the proper chemical balance in cooling tower water prevents corrosion, scaling, and biological growth. Water chemistry control involves adjusting pH levels, adding corrosion inhibitors, and using biocides to manage microbial contamination. Regular water quality testing and treatment adjustments are necessary to keep the system running efficiently and safely. Proper water chemistry control enhances the longevity of the cooling system and ensures optimal performance.
Optimize your cooling water management with M4 Knick‘s advanced Conductivity Sensors. Tailored for any system, these sensors ensure precise water chemistry control.
Conclusion.
Cooling water systems are the lifeblood of many industrial processes and are crucial in maintaining operational efficiency and safety. Whether using once-through cooling, cooling towers, or open recirculating systems, managing the challenges of leaks, corrosion, scaling, biological contamination, and hydrocarbon vapours is essential. By understanding and addressing these issues, industries can ensure the reliability and effectiveness of their cooling water systems, safeguarding both their operations and the environment.
Be the first to read our articles
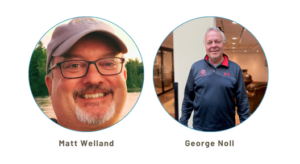
Written by Matt Welland – “Key Account Manager”
& George Noll -“Technical Sales Representative – Retired“
Write to Matt at: wellandm@novatech.ca