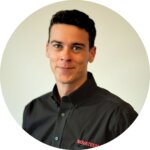
Ultra Pure Water (UPW) is not just a component—it's a pivotal necessity in industries where even minor impurities are unacceptable. From semiconductor manufacturing to pharmaceuticals, the demand for UPW underscores its importance in modern technology and healthcare. This article dives into the specifics of how UPW plays a critical role in maintaining high-quality standards and operational excellence.
What you’ll learn:
- Significance of UPW in Critical Industries: Understand its impact on product quality and system reliability.
- Real-Time Monitoring Systems: The benefits of deploying online measurement tools for continuous quality assurance.
- Total Organic Carbon (TOC) Monitoring: Importance of TOC in detecting organic contaminants in UPW.
- Conductivity Measurement: How conductivity assesses ionic purity and its importance for process efficiency.
- Boron Measurement Techniques: The role of boron analyzers in maintaining the integrity of UPW systems.
The Critical Role of Ultra Pure Water.
UPW is the backbone of industries that cannot tolerate any compromise on purity. Semiconductor manufacturers depend on UPW to avoid circuit failures caused by the slightest particulate contamination. In pharmaceuticals, UPW ensures that no impurities compromise drug safety and efficacy. This high level of purity is not just about meeting standards but ensuring consistent performance, high yields, and compliance with stringent regulatory frameworks.
Advancements in Real-Time Monitoring of UPW.
Modern industries are increasingly implementing online systems to monitor UPW quality parameters continuously. These systems measure total organic carbon (TOC), conductivity, and boron levels, providing immediate feedback on water quality. This real-time data is crucial for:
- Detecting deviations from purity standards swiftly.
- Enabling prompt corrective actions to mitigate risks of contamination.
- Optimizing water treatment processes to enhance operational efficiency.
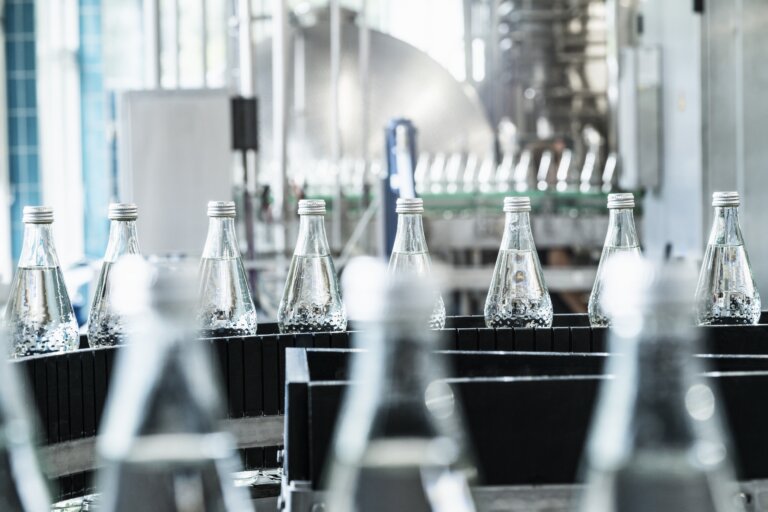
Total Organic Carbon (TOC) Monitoring.
TOC monitoring is indispensable in UPW applications. Trace organic compounds, even at minimal levels, can significantly affect product quality. TOC analyzers help detect these organic contaminants early, preventing potential damage in sensitive environments like semiconductor and pharmaceutical manufacturing.
Conductivity Measurement in UPW.
Conductivity measurement is a vital part of maintaining UPW’s ionic purity. It helps ensure that dissolved inorganic impurities, such as salts and metals, are minimized to avoid damage to high-precision equipment. On-line conductivity measurements help maintain the necessary purity levels to prevent inefficiencies and potential operational failures.
Boron Measurement: Ensuring System Integrity.
Boron analyzers play a crucial role in predicting the exhaustion of mixed-bed ion exchange resins, a common component in UPW systems. By monitoring boron levels, facilities can optimize electro-deionization performance and control the levels in the polishing loop. This monitoring is essential to prevent silica leakage into the UPW, safeguard the system from potential disruptions, and maintain consistent water purity.
Conclusion.
Ultra-pure water is essential in industries where purity is not just required but critical for success. With the right technologies and strategies for monitoring and maintaining UPW, industries can achieve compliance with rigorous standards and unparalleled operational excellence. This installment in “The Journey of Water” series highlights the indispensable nature of UPW and the sophisticated techniques used to preserve its purity in demanding industrial applications.
Be the first to read our articles
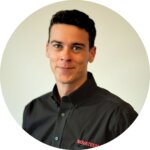
Written by Félix Lalande-Hendershot
Technical Sales Representative
Write to Félix at: lalandehf@novatech.ca