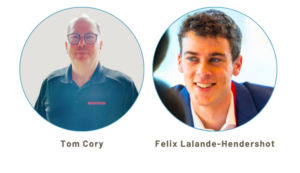
Written by Tom Cory & Felix Lalande-Hendershot
Technical Sales Representatives
July 31, 2024
In this installment of our "Journey of Water" series, we explore the critical role of Boiler Feedwater—a fundamental element in steam generation systems. This discussion will give you an in-depth understanding of the complexities and solutions involved in maintaining high-quality feedwater to ensure optimal performance and longevity of boiler systems.
What you’ll learn:
The Importance of High-Quality Boiler Feedwater
Key Treatment Processes for Feedwater
The Role of Chemical Additives in Feedwater Maintenance
Monitoring and Control: Ensuring Feedwater Quality
Strategies to Manage Total Organic Carbon (TOC) in Boiler Systems
The Importance of Sample Conditioning in Water Analysis
Introduction to Boiler Feedwater.
Boiler feedwater is essential for the efficient operation and health of steam-generating systems. Properly treated feedwater ensures that boilers can operate at peak efficiency while preventing common issues such as corrosion, scale formation, and equipment degradation. Feedwater quality directly influences steam systems’ energy efficiency and operational costs, making proper management crucial for any facility reliant on steam power.
Enhance boiler feedwater quality with the SE 615 Memosens Conductivity Sensor from M4 Knick. Achieve precise monitoring for optimal boiler performance and longevity. See how this sensor optimizes feedwater processes.
Understanding the Treatment of Boiler Feedwater.
To achieve optimal performance and protect boiler components, feedwater must undergo a series of treatment processes designed to remove impurities and condition the water for use in high-pressure environments. These treatment methods include:
- Filtration and Chemical Treatment
Feedwater is typically filtered to remove physical impurities such as dirt, debris, and suspended particles. Following filtration, chemical treatment processes are applied to address dissolved minerals and gases. Hardness ions, which can cause scale and reduce heat transfer efficiency, are neutralized using specific chemical agents. This not only protects heating surfaces but also enhances the overall efficiency of the boiler system.
- Deaeration: Oxygen Removal
Oxygen in boiler feedwater can lead to severe corrosion if not adequately managed. Deaeration techniques, often combined with the use of oxygen scavengers, effectively remove dissolved oxygen, thereby protecting boiler internals from oxidative damage. This process is essential for extending the boiler’s life and maintaining its efficiency.
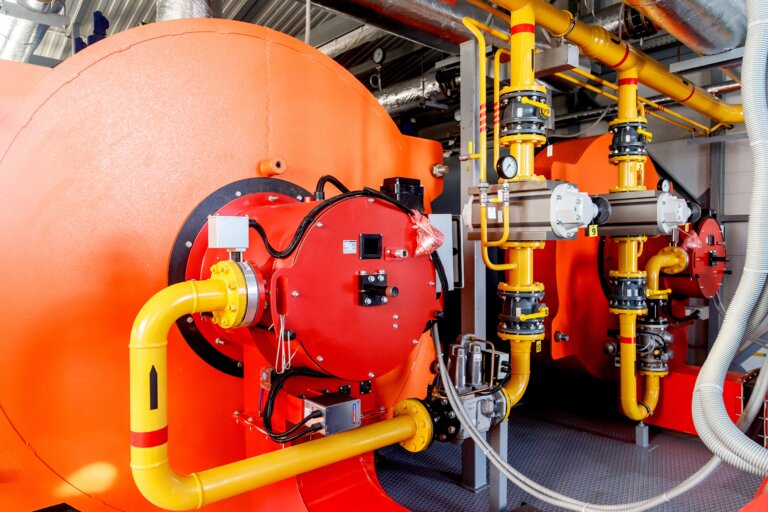
The Role of Chemical Additives.
Chemical additives play a pivotal role in maintaining the quality of boiler feedwater. These additives include:
- pH Adjusters: To combat corrosion, maintaining the pH of feedwater within the optimal range of 8.5 to 9.5 is crucial. pH adjusters stabilize the pH levels, providing a protective environment for boiler components.
- Scale Inhibitors: These chemicals prevent scale formation on boiler tubes, which can insulate heat transfer surfaces and decrease efficiency. By inhibiting scale, these additives help maintain the heat transfer rates required for efficient operation.
- Oxygen Scavengers: Employed to eliminate residual oxygen post-deaeration, these additives further reduce the risk of corrosion, particularly in the boiler’s heat exchange surfaces.
Monitoring and Control Techniques.
Continuous monitoring of feedwater quality is imperative for the successful operation of boiler systems. Key parameters monitored include:
- Conductivity: Reflects dissolved solids’ concentration and helps manage scale formation.
- Dissolved Oxygen Levels: Essential for assessing the effectiveness of deaeration and oxygen scavenging processes.
- pH Levels: Regular monitoring ensures the feedwater remains within the optimal pH range to prevent corrosive conditions.
- Total Organic Carbon (TOC): Monitoring TOC levels is crucial for detecting organic contaminants that could lead to fouling and corrosion. Effective management of TOC through continuous monitoring enables timely adjustments to treatment processes, ensuring the integrity and efficiency of the boiler system.
Sample Conditioning for Representative Results.
Using Steam & Water Analysis Systems (SWAS) conditioning panels is vital in precisely controlling boiler feedwater. These panels are integral to maintaining the integrity and reliability of steam and water samples. By regulating temperature and pressure, stabilizing chemical compositions, and removing particles, SWAS conditioning panels ensure the accuracy of monitoring water quality, chemical treatment levels, and corrosion rates in power plants and boilers. Their role extends beyond mere measurement; they enhance safety by providing a controlled environment for handling high-temperature, high-pressure samples and facilitating efficient manual sample collection for further lab analysis.
Optimize your SWAS operations with Novatech’s Compact Conditioning Panel. Ensure accurate and reliable feedwater analysis with our expertly designed solution.
Conclusion.
High-quality boiler feedwater is indispensable for maintaining efficient, reliable, and long-lasting boiler systems. Through advanced treatment processes, continuous monitoring, and the strategic use of chemical additives, professionals can ensure that their steam generation systems operate at peak efficiency while minimizing operational costs and environmental impact.
Be the first to read our articles
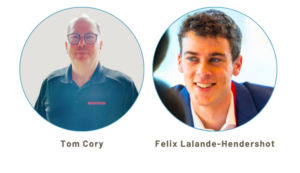
Written by Tom Cory & Felix Lalande-Hendershot
Technical Sales Representatives.
Write to us at: coryt@novatech.ca & lalandehf@novatech.ca